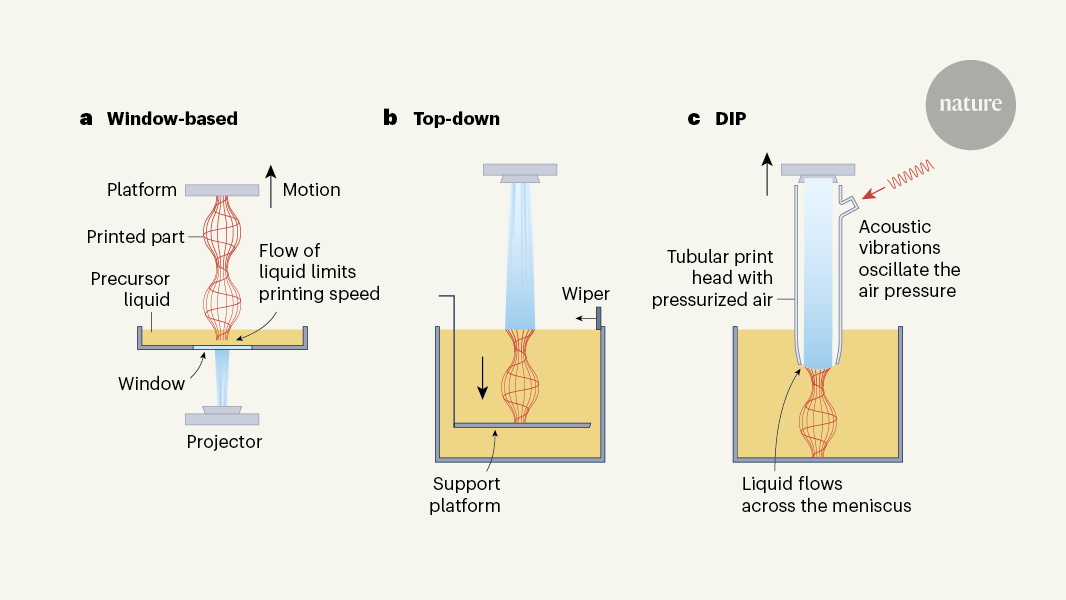
Dynamic interface printing
A 3D-printing strategy to rapidly map structures and surfaces for in situ imaging using light patterns projected onto liquid crystals (H.T.)
H.T. is an inventor ofCAL which is an Additive Manufacturing Process which the authors of the article claim has several advantages. H.T. carries out research, holds funding related to CAL, and holds several patents on CAL and a small number of shares in a company that holds a licence to practice CAL.
3D printing innovations promise to change the way objects are made to serve a broad range of industries. Digital light manufacturing is an expanding category of 3D-printing processes that use patterns of light projected onto a liquid to create solid structures. The goal is to develop processes to rapidly print features at tiny scales using a wide range of materials, with excellent surface finishes and ideally suited for industrial applications, potentially up to a scale of many centimetres. The quality of the objects is reduced due to light patterns in the liquid and practical issues limiting the speeds of current processes. Writing in Nature, Vidler and colleagues propose a 3D-printing strategy that could solve these problems.
A variety of print speeds and optical dose combinations were tested to find the ideal space for the DIP. For each combination, triplicate (n = 3) structures with dimensions of 5 × 5 × 15 mm3 were printed, with successful outcomes being defined by the presence of a sharply delineated structure and a smooth surface finish. The structures that did not meet these requirements either because they were only partially resolved or because no structure had been produced were removed from the map. Generally, the print-speed parameter space was not only constrained by the optical dosage but also by the rate at which new material can ‘wet’ the interface. The interface to the underlying structure can be fluidly pinned as the rate of polymerization exceeds the mass transport of new material.
A second system iteration was developed for in situ imaging, with modifications to allow the printing container to move relative to a stationary probe (Supplementary Fig. 3). A custom CoreXY motion system and a ball-screw linear stage were included in the system. In situ imaging was facilitated by a blue reflective dichroic mirror (35-519, Edmund Optics) and a 50:50 beam splitter for illumination (43-359, Edmund Optics). Illumination was provided either coaxially or with a custom well-plate holder with a red collimated backlight. The motion components and printing head were enclosed within a heated chamber to maintain optimal temperatures. Continuous HEPA filters were used to maintain sterility as well as surface sanitization with 70% ethanol and UV-C before use.
Direct volume manipulation of the air volume inside the print head allowed acoustics to be achieved. The approach was simple. The set up consisted of a 3 inch voice coil driver which was attached to an enclosed 3D printed manifolds containing an inlet and outlet port. 1c,d The voice coil was driven by a commercially available amplifier (Adafruit, MAX9744) using the supplied auxiliary port, with specified waveforms sent by the MATLAB GUI. When possible, there was a range of up to 500HZ with either a fixed or Transient Frequency. For each degree of freedom, it was possible to specify a waveform for the acoustic modulation to be synchronized with the other motion, optical and pressure control.
Mixture of GelMA, tartrazine and N-hydroxysuccinimide: preparation and refrigeration of gelMA and sodium alginate
In this study, different concentrations of PEGDA were used, ranging from 10% to 100% w/v. The required weight fraction was dissolved in the corresponding volume fraction of 40 C deionized water and thoroughly mixed for 10 minutes. The mixture was stirred until complete dissolution after 0.21% and 0.035 w/w of tartrazine and LAP were added. When needed, the materials were kept in Falcon tubes.
A solution of 500 mg of phenylbis(2,4,6-trimethylbenzoyl) phosphine oxide (511447, Sigma) and 50 g of 1,6-hexanediol diacrylate (246816, Sigma) was prepared by warming the mixture to 40 °C and stirring for 30 min. The Sudan I was added in various amounts to control the resolution. The materials were then stored in light-safe Falcon tubes until required.
GelMA was synthesized following a previously reported protocol56, yielding a degree of substitution of 93% (confirmed by nuclear magnetic resonance). The 10% solution was prepared by dissolving 1 g of GelMA in the cell culture media at 37 C. After complete dissolution of the GelMA, 3.5 mg of tartrazine and 25 mg of LAP were added to the solution, which was maintained at 37 °C until complete dissolution. The mixture was kept in the refrigerated Falcon tubes until needed after being passed through a sterile filter and stored in a bio safety cabinet.
Norbornene-functionalized sodium alginate was synthesized based on a previously reported protocol57. In 500 grams, 0.1 M 2-(N-Morpholino) ethane-sulfonic acid buffer was dissolved with a fixed pH of 5.0. Then, 9.67 g of 1-ethyl-3-(3-dimethylaminopropyl) carbodiimide•HCl, 2.90 g of N-hydroxysuccinimide and 3.11 ml of 5-norbornene-2-methylamine were added. The acidity was fixed at 7.5 with one millionth of a second. The reaction was carried out at room temperature for 20 h. The mixture was dialysed against the water before lyophilization. The degree of norbornene functionalization was determined to be 16.2% by 1H nuclear magnetic resonance. A 7% w/v sodium alginate solution was prepared by dissolving 1 g of the sodium alginate in 14.29 ml of phosphate-buffered saline solution. Next, 5 mg of tartrazine, 36 mg of LAP and 122.7 µl of 2,2′-(ethylenedioxy)diethanethiol were dissolved in 5.59 ml of phosphate-buffered saline, added to the sodium alginate solution and mixed until it was homogeneous. The pH was adjusted with 1 M NaOH until the solution was visibly opaque.
A solution of 50 mg of phenylbis(2,4,6-trimethylbenzoyl) phosphine oxide (511447, Sigma) and 5 g of diurethane dimethacrylate (436909, Sigma) was prepared by warming the mixture to 45 °C and stirring for 30 min. To remove trapped air bubbles, the mixture was transferred to a light-safe Falcon tube and centrifuged at 4,000 rpm for 10 min to remove residual air bubbles.
Source: Dynamic interface printing
Cell Viability of a 3D Printing System for the Development of the Kidney Bioinfra-Cell: Model and Experiment
The cells that were used in the determination of the cell viability of the 3D printing system were human embryo fibroblasts. The model of the kidney and the cell viability results were obtained with a cell solution of 7.2 million cells per deciL. To determine cell viability, a thin 500 m wall was printed, with enough media to cause no cell death, but enough to cause a dead/dead viability/toxicity kit to be used. After 24 h, it was possible to see if the technique was viable with three structures printed. The cell viability was determined at three locations, with the average of all collection points being the total viability.
To create the cell-loaded bioink, the GelMA solution was warmed to 37 °C followed by the resuspension of cells into the solution. When not in use, the solution was put in a water bath at a temperature of 37 C. The printing process involved pipetting approximately 3 ml of the GelMA ink into a single well of a 12-well plate and lowering the print head into the well. The suspension and cell settle were mitigated during each printing with the use of acoustic wave propagation (50 hertz, P 0.1). As the printed wall had a high aspect ratio and low contact area, a relatively slow print velocity of Vz = 150 µm s−1 was used to mitigate unwanted detachment. This resulted in an object creation time of approximately 30 s.
The curved surface used for this work has differences in its discretization compared to a traditionally flat construction surface. There is a detailed explanation of the process in the Supplementary Information. There will be a brief restation of the main components here. The Laplace pressure difference was used to determine the general shape of the interface. Here, we used axisymmetric print containers that can be found easily if you substitute the general expressions for principal curves. The capillary length (l=\sqrt{\gamma /\rho g}), where γ is the material surface tension, ρ is the material density and g is the acceleration due to gravity, was used to normalize the radial and vertical coordinates of the interface as (x=r/l) and (y=z/l). The equation for the interface shape was the ordinary differential equation.
This equation can be readily solved using numerical integration with appropriate boundary conditions (Supplementary Information section 4). However, using this method would require numerical integration for the steady-state case, and moreover, we would need to solve each intermediate state during compression with the associated boundary conditions. We, instead, opted to approximate the solution using cubic Bézier curves for the steady-state case and approximating the compressed profiles by geometrically deforming the Bézier curve while ensuring volume equivalency (Supplementary Information section 7). The large number of intermediate surfaces within the Transient region speed this up. The central z axis of the print head was the point of focus for the half-profile. This produced a sequence of surfaces starting at the compressed state and transitioning to the steady-state interface profile. The projection of the voxel grid was determined by considering the distance between the grid and the surface array. Reconstruction accuracy was validated by ‘replaying’ the projections over an empty voxel array and computing the Jaccard index between the reconstructed voxel array and the input voxel array (Supplementary Information sections 8 and 9).
To determine our theoretical optical model (Supplementary Information section 10), we employed a similar approach to Behroodi et al.59, who modelled the in-plane resolution as the spatial convolution of the point spread function (({\rm{PSF}}(x,y))) and the micro-mirror spatial arrangement ((f(x,y))), where (f\left(x,y\right)\ast {\rm{PSF}}\left(x,y\right)={\int }{-\infty }^{\infty }{\int }{-\infty }^{\infty }f({\tau }{1},{\tau }{2})\,\cdot \,{\rm{PSF}}\left(x-{\tau }{1},y-{\tau }{2}\right)\,{\rm{d}}{\tau }{1}\,{\rm{d}}{\tau }{2}), and τ1 and τ2 represent spatial shifts, summed over all possible displacements, during convolution. To determine the effective delivered energy and depth of cure across the meniscus, a ray incident on the meniscus was decomposed into reflective and transmissive components, described by a transmissive efficiency η, dependent on the relative angle and refractive index mismatch (\eta ({n}{1},{n}{2},\hat{{\bf{u}}},\hat{{\bf{n}}})). The normal plane for the air and liquid is (hatbfu) while n1 and n2 represent the air and liquid. The energy intensity along the transmissive vector ({\gamma }{z}) was approximated as a material-dependent Beer–Lambert decay ({\mathcal{H}}({{\boldsymbol{\gamma }}}{x},{{\boldsymbol{\gamma }}}{y},{{\boldsymbol{\gamma }}}{z})\,=\,\eta ({n}{1},{n}{2},\hat{{\bf{u}}},\hat{{\bf{n}}})\cdot \hat{{\bf{E}}}\,\exp \left(\frac{-{{\boldsymbol{\gamma }}}{z}}{{\varepsilon }{{\rm{d}}}\left[D\right]+{\varepsilon }_{{\rm{i}}}\left[S\right]}\right)) (Supplementary Information section 11), where, εd and εi are molar absorption coefficients of the photoinitiator and the light absorber, respectively, and D and S are the concentrations of the photoinitiator and light absorber of the photopolymer resin, respectively. As the interface is curved, the effective resolution is spatially dependent on the local height of the meniscus relative to the focal plane. For each pixel at the focal plane, we mapped its local coordinate to the corresponding coordinate on the meniscus surface, resulting in a contour map of the effective pixel size across the interface. This map was used to theoretically predict the accurate area fraction the contingent on print head’s size and material properties (Supplementary Information section 12).
Many analytical approaches were used to understand how the meniscus caused the formation of capillary-gravity waves. The velocity scaling law for capillary-gravity waves depends on the dominance of capillary or gravity-driven effects. The wavenumber is related to the wavenumber of the capillary waves. We, therefore, show that ({(\lambda /{l}{{\rm{cap}}})}^{2}) is a unitless quantity that relates the dominance of surface tension and acoustic parameters on the flow magnitude (Supplementary Information section 14). Here, lcap denotes the capillary length of the material. Thus, the flow velocity U scales as (U\propto \frac{{h}{0}^{2}\rho g\phi }{\lambda \mu }) for ((\lambda /{l}{{\rm{cap}}}) > 1) and (U\propto \frac{{h}{0}^{2}\gamma \phi }{{\lambda }^{3}\mu }) for ((\lambda /{l}_{{\rm{cap}}}) < 1), where, h0, ϕ and μ represent the surface perturbation, wave amplitude and viscosity, respectively. Supplementary Fig. 19 shows the effect of material and acoustic parameters on velocity scaling.
PIV was used to understand the 3D flow field produced below the air–liquid boundary. The footage was shot using a high-speed camera. particles during excitation, both normal and orthogonal to the air–liquid boundary. The captured video sequence was used to perform particle tracing and velocity reconstruction. It is possible to find the parameters and methodology in Supplementary Information section 18. The side and top-down profiles are shown. 3c–e and Supplementary Figs. 8 and 9.
To determine the transient interface restabilization in the bulk flow, high-speed photography under a uniform backlight was captured at 5,000 fps (Supplementary Fig. 7). The first thing you have to do to determine restabilization is segment the meniscus edges and watch the video stream to see if it strays from its normal point of view. The interface settling time was determined by applying a criterion set at 1/e2.
The material influx rate with and without acoustic excitation was determined by filling a glass cuvette with materials doped with black dye to prevent light transmission. When the air–liquid Boundary formed against the base of the Cuvette, a light from the red backlight came to be seen by a camera. The material influx rate was measured by raising the air–liquid boundary with and without acoustic excitation and tracking the influx of dyed material, which occluded the backlight transmission (Fig. 3f and Supplementary Information section 20 and Supplementary Fig. 11).
Source: Dynamic interface printing
Micro computed tomography of hydrogel, hydrogel and other hydrogel samples for high-conductivity helium-ion microscopy
The voxel size of 10 m3 was used for the images, along with a 200 A tube current and 8 min scanning time. For hydrogel samples, the structures were briefly dried with tissue paper and mounted into a Falcon tube for imaging. The structures were placed on a plastic cap to give them a good contrast between printed and supporting materials. An STL surface mesh was extracted and imported into Keyshot 11 (Keyshot, Luxion) to render the final micro computed tomography representation.
The images were captured with a 4 or 10 objective. The images were used in the software to create large-format images for constructs larger than the goal field of view. Once the fluorescence images were acquired, cell-counting was performed on each live/dead image pair using a custom MATLAB script.
Scanning electron microscope images were acquired on a FlexSEM 1000 (Hitachi High Technologies). The structures on the glass slides were mounted on the microscope stage without further sample preparation. The samples did not have a conductive coating applied. The microscope was used in variable-pressure mode. The images were obtained using the ultra-variable detector. The large structures required a covering field of view of at least 50 millimetres and several images were collected in a tiled manner.
Helium-ion microscopy images were acquired with a Zeiss NanoFab using a helium source. During imaging, the flood gun was used to actively neutralize the surface, thus removing the need for a conductive coating. All structures were imaged using an accelerating voltage of 30 kV, a beam current of between 1 and 2 pA, and a field of view of 1,100 µm. Structures were printed directly onto a silanized glass slide and were mounted on the stage using the integrated mounting clips. To facilitate the capture of structures larger than the field of view, several images were taken and later stitched using ImageJ/Fiji.