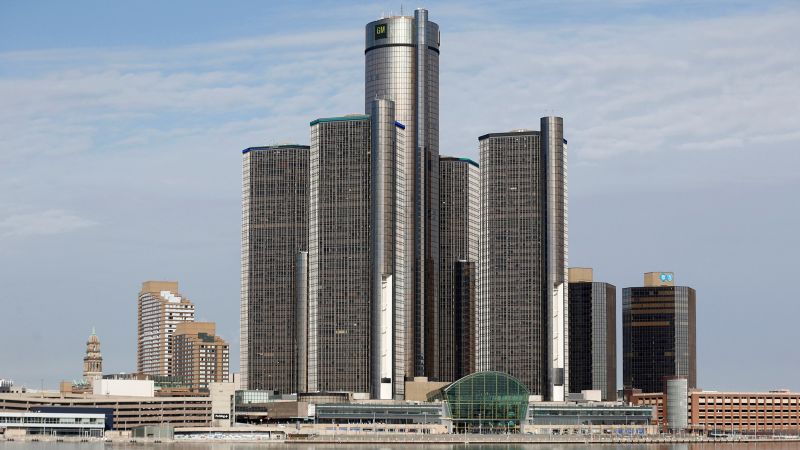
There were EV battery plants in the U.S. in 2022, they were worth $73 billion
The Connection Between China, the U.S. Battery Industry, and the Southeast: The Case for Electric Vehicles in Georgia and the United States
It’s hard to keep track of the plants that make the enormous batteries for electric vehicles if you follow the auto industry.
Did you know about KORE Power in Arizona? Is there a connection between Stellantis and South Korea in Indiana? The Chinese project in Michigan, the Norwegian one in Georgia, the Japanese one in South Carolina?
Or, if you don’t like the idea of $5 billion for an electric vehicle and battery project in Georgia, what about a billion dollars? No, not that one — the other one.
Pressure is building on companies involved with battery production in order to reduce reliance on China and create American jobs. China currently hosts as much as 90% of global production of some key components for batteries.
In January of last year, the then-president of Volkswagen of America told NPR that moving production was beneficial to the company. “It’ll be a dramatic, dramatic, dramatic help having the supply chain localized, having the car here and, frankly, just having enough production slots.”
The cost of conversion to electric has been amortized in the last year, with batteries from a new SKI plant in Georgia being used for the new line at the Chattanooga plant.
The Southeast has been dubbed the “battery belt” due to the number of new U.S. projects going up there. But Tom Taylor, an analyst with Atlas, says the trend is geographically wider than that.
He says that they’ve seen announcements all over the country. These are some of the largest economic development projects that the state’s history has ever seen.
The Future of the Automotive Industry: GM Financial and the Fate of the Old Battery Plant, a Large-Scale Autonomous Collider
Mary Barra had to explain the slow pace of production at the new battery plant in Ohio on a recent call with investors.
“Let’s step back and recognize that the Ohio plant is the size of 30 football fields, and it will employ over 1,000 people,” she said. It has taken a little longer than expected to make sure all of our people are trained.
And that’s particularly concerning to some critics, because not all of those billions of dollars are coming from companies — a big chunk of it is footed by taxpayers.
Good Jobs says more than 14 billion in state and local subsidies went to electric vehicle plants and battery factories. First, which has criticized both the size of the subsidies and the lack of transparency around them.
Most of the announcements tallied by Atlas predated a national climate bill that passed this summer, which included hefty incentives for U.S.-based electric vehicle manufacturing.
The largest US automaker also said Tuesday it is buying a $650 million equity stake in Lithium Americas, which will give it access to the raw material needed to build batteries to power 1 million electric vehicles a year in the first phase of production.
It expects to have strong earnings of between $8.7 billion and $10.1 billion in the next twelve months, though it might fall a bit from the posted levels. But company CFO Paul Jacobson said its automotive business is expected to remain strong, with much of the decline likely to be at GM Financial. That’s due to the hit it will take from higher interest rates and the sinking value of used cars, as well as the higher interest rates resulting in an accounting hit to pension earnings.
“I don’t think there’s any surprise there’s increasing competition in the EV space,” he said. The customers say we are priced well because of the demand.
The company opened a new battery plant last year, as well as two more under construction and a fourth planned soon. GM has a target to build 400,000 EVs through the middle of 2024, and 1 million annually by 2025.
GM said it will reduce its staff in 2023, part of its effort to cut $2 billion in costs over the next two years. company officials stressed that GM wouldn’t be shrinking through layoffs, unlike some major companies that have recently announced layoffs. attrition would handle the reduction.
GM has 167,000 employees globally, with 124,000 in North America. That includes more than 42,000 members of the United Auto Workers union. The average profit share bonus will be up 25% to $12,750 from 10,250 the year before.
Ford Motors: Exploring the Michigan Location for the LFP Lithium Iron-Phosphate Battery Plant in the U.S.
Ford considered sites outside the US for this battery plant but settled on the Michigan location because of the tax credit rules, said Lisa Drake, Ford’s vice president of EV industrialization.
The $430 billion inflation reduction act that was passed in August restructures how the EV tax credits are allowed. Under the new law, consumers buying an electric vehicle will be eligible for tax credits of varying amounts, depending on whether the vehicle itself, as well its batteries and battery components, were manufactured and the battery minerals extracted in the US.
She said that she thought the IRA did what it was intended to do. “And it allowed the United States to capture 2,500 fantastic technical jobs and all the indirect jobs that go with it plus the future growth.”
The plant will make lithium iron phosphate batteries, better known as LFP (lithium ferro-phosphate), batteries. The elements that can be hard and expensive to extract from the earth are used in this type of battery.
Ford claims it is the first automaker to commit to developing two separate battery chemistries for its EVs at the same time: lithium iron phosphate (LFP) and nickel cobalt manganese (NCM). (Tesla is also producing vehicles with LFP batteries.)
Most of today’s EV use NCM chemistries, which are used in the production of lithium-ion batteries. But NCM also has a lot of baggage, due mostly to cobalt, which has been called the “blood diamond of batteries” because it’s been mined in a way that’s endangered child workers and wrecked the environment in the Democratic Republic of Congo.
“They are exceptionally durable and they tolerate more frequent and faster DC fast charging,” Lisa Drake, vice president of EV industrialization at Ford model e, the company’s EV division, said during a briefing with reporters Monday. “And they actually perform best when they’re being charged from zero to 100 percent regularly. It’s ideal for customers who want to charge quickly and then drive all the way to empty.
Drake explained that the addition of LFP batteries to the mix was due to a desire to reduce costs. She said that the recipe to create one of the lowest-cost US-produced batteries would come from this plant.
Reducing costs is certainly top of mind for the automaker, which had a particularly rough earnings this past quarter. According to Jim Farley, the company left $2 billion in profits on the table, blaming poor execution and entrenched issues in our industrial system.
Rumors of the new factory have been swirling for months. One of the places Ford considered building it was one of the poorer parts of Virginia, a part of the South where there are a lot of battery plants. Up to 2,500 new jobs would have been created in the project, which building batteries for Ford’s electric vehicles. But Glenn Youngkin, the state’s Republican governor, rejected the project because of the involvement of CATL, citing the influence of China’s communist government.